As an operations manager, I often get asked a key question. It’s about the best ways to make manufacturing processes better and keep improving. This question is central to our discussion, as we dive into the power of industrial management. We’ll look at Lean Manufacturing, Six Sigma, Kaizen, and Total Quality Management (TQM).
In today’s fast-paced world, companies must keep improving their production to stay competitive. By using tested methods and the right tools, they can cut waste, make workflows smoother, and foster a culture of constant improvement. This leads to lasting growth and staying ahead in the market.
Key Takeaways
- Discover the principles and benefits of continuous improvement in manufacturing operations
- Explore key industrial management frameworks like Six Sigma, Lean, Kaizen, and TQM
- Understand how to measure and track progress using essential performance indicators
- Learn strategies for implementing and sustaining continuous improvement initiatives
- Gain insights from real-world case studies showcasing the impact of these methodologies
Introduction to Continuous Improvement
Continuous improvement is a key way for companies to get better over time. It focuses on making small changes to improve how things are done. The goal is to make things more efficient, better quality, and more satisfying for customers, while saving money and reducing waste.
Definition of Continuous Improvement
Continuous Improvement, or Kaizen, is a Japanese way of managing that focuses on small steps to get better. It uses the PDCA cycle to keep improving and getting better. This cycle is all about making things better step by step.
Principles of Continuous Improvement
- Focus on process improvement rather than just problem-solving
- Involve all employees in the improvement process
- Emphasize small, incremental changes rather than large, radical changes
- Encourage a culture of continuous learning and adaptability
- Utilize data-driven decision making and Quality Management tools
Benefits of Continuous Improvement
Companies that use Continuous Improvement see many benefits. These include:
- Increased efficiency and productivity
- Improved quality and reduced defects
- Enhanced customer satisfaction
- Reduced costs and waste
- Increased employee engagement and morale
- Stronger competitive advantage
By always trying to get better, companies can cut waste, make things smoother, and keep up with market changes. This leads to lasting success and growth.
“Continuous Improvement is not about the things you do well – that’s work. Continuous Improvement is about removing the things that get in the way of your work. The headaches, the things that slow you down, that’s what Continuous Improvement is all about.”
Key Performance Indicators for Continuous Improvement
To make continuous improvement work, you need to measure its success with Key Performance Indicators (KPIs). These KPIs should show how well your processes are doing in key areas. By tracking the right KPIs, you can understand your progress and make smart choices to keep improving.
Here are some important KPIs for your continuous improvement journey:
- Overall Equipment Effectiveness (OEE): This metric shows how well your equipment is used. It looks at availability, performance, and quality. It helps you see if your operation is running at its best.
- Productivity Rate: This KPI shows how much you produce compared to what you use, like labor hours. It helps you find ways to work more efficiently.
- Defect Rate: It tracks how many products don’t meet quality standards. This shows where you can improve to make fewer mistakes.
- On-Time Delivery: This KPI checks if you’re meeting customer deadlines. It’s key for keeping customers happy and loyal.
- Inventory Turnover: It shows how well you manage your stock. It helps you find ways to use your money better and avoid too much stock.
By watching these and other KPIs closely, you can really understand how your organization is doing. This lets you make smart choices to keep improving, using tools like DMAIC and Six Sigma.
“Effective measurement is the foundation of continuous improvement. What gets measured, gets managed.”
Gestion Industrielle: Methodologies and Tools
In the world of industrial management, Six Sigma and Total Quality Management (TQM) stand out. These methods have changed how companies improve their processes and keep getting better.
Six Sigma DMAIC Process
The Six Sigma DMAIC (Define, Measure, Analyze, Improve, Control) process is a key way to make things better. It was started by Bill Smith at Motorola in 1986. It uses data to check if processes are working well.
The aim is to make a process so good that it has almost no mistakes. This means fewer than 3.4 defects per million items made.
- Define the problem and set clear goals
- Measure the current performance and collect relevant data
- Analyze the data to identify the root causes of problems
- Improve the process by implementing solutions
- Control the improved process to maintain the gains
Total Quality Management (TQM)
Total Quality Management (TQM) is a big-picture way to manage quality. It’s all about making things better, pleasing customers, and getting everyone involved. TQM sees the whole company as one big team working together.
- Customer-centric focus
- Continuous process improvement
- Empowerment and involvement of all employees
- Data-driven decision making
- Collaborative teamwork
Using Six Sigma, DMAIC, and TQM, companies can really boost their quality and efficiency. This makes them more competitive in the market.
Lean Manufacturing Principles
Lean manufacturing, also known as “production au plus juste” in French, is a way to improve continuously. It was first described by James P. Womack, Daniel Jones, and Daniel Roos in “The Machine That Changed the World.” They based it on their work in a Toyota factory, focusing on five main principles.
- Value – Clearly define the value from the customer’s perspective.
- Value Stream – Identify the value stream and eliminate waste.
- Flow – Ensure a continuous flow of production.
- Pull – Implement a pull system, where production is driven by customer demand.
- Perfection – Continuously strive for perfection through ongoing improvement.
Lean manufacturing aims to cut down on production times and improve response times. It focuses on making things more efficient and reducing waste. It also makes sure production matches demand closely.
The seven wastes in Lean manufacturing are overproduction, over-processing, transportation, excess motion, waiting, making defective products, and superfluous inventory. Lean manufacturing was heavily influenced by Toyota’s Production System from the 1950s and 1960s. It emphasizes just-in-time inventory and quality control.
It has been used to boost efficiency, cut down on inventory costs, and increase productivity and profits. For Lean manufacturing to work well, you need to forecast demand accurately, have high-quality processes, and reliable suppliers.
Lean Principle | Description |
---|---|
Value | Clearly define the value from the customer’s perspective. |
Value Stream | Identify the value stream and eliminate waste. |
Flow | Ensure a continuous flow of production. |
Pull | Implement a pull system, where production is driven by customer demand. |
Perfection | Continuously strive for perfection through ongoing Continuous Improvement. |
Lean manufacturing is all about continuous improvement in production. It encourages employees to suggest ways to improve efficiency. Key concepts like Value Stream Mapping, Demand-based (pull) system, Continuous improvement, and Measurement through KPIs and Visualization help companies become more agile, innovative, and efficient.
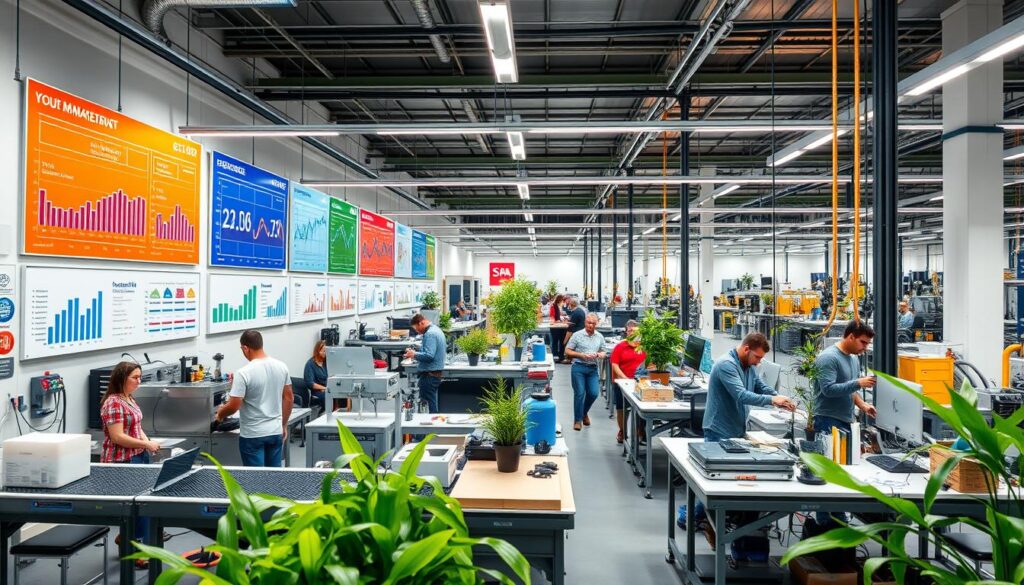
Kaizen Methodology
Kaizen is a Japanese term that means “change for the better” or “continuous improvement.” It’s a powerful way to get everyone involved in solving problems. It’s all about making small changes over time to get better.
The Five Kaizen Principles
- Teamwork: Kaizen creates a team environment where everyone shares ideas and works together.
- Personal Discipline: It teaches employees to own their work and keep improving themselves.
- Improved Morale: Kaizen boosts morale by empowering employees and celebrating their small wins.
- Quality Circles: It uses quality circles for employees to meet and solve work-related problems.
- Suggestions for Improvement: Kaizen encourages everyone to suggest improvements, big or small, and rewards them.
Kaizen is used in many fields like manufacturing, healthcare, and services. It fits well with Continuous Improvement and Waste Elimination. Adding Process Mining to Kaizen makes it even more effective for excellence.
“Kaizen is a way of life, a continuous journey of small steps towards perfection.” – Masaaki Imai, the founder of the Kaizen Institute
By following the Kaizen Principles, companies can see big improvements. They can get better at what they do, make customers happier, and stay competitive.
Six Sigma vs Kaizen: Choosing the Right Approach
Organizations have two main choices for improving operations: Six Sigma and Kaizen. Both aim to boost performance but differ in their methods.
Six Sigma uses data to cut down on defects and improve quality. It follows the DMAIC process to find and fix problems. It aims for fewer than 3.4 defects per million opportunities, focusing on detailed analysis and financial gains.
Kaizen, on the other hand, is a Japanese way of making small, ongoing improvements. It uses the 5S principles to improve continuously. Unlike Six Sigma, Kaizen encourages everyone to contribute to improvement.
The choice between Six Sigma and Kaizen depends on the organization’s needs. Six Sigma is good for big, complex problems needing detailed analysis. Kaizen works well for small, quick fixes that employees can handle.
The best approach often combines both Six Sigma and Kaizen. This mix uses their strengths for full Process Optimization and Continuous Improvement Methodologies.
Characteristic | Six Sigma | Kaizen |
---|---|---|
Approach | Data-driven, analytical | Incremental, employee-driven |
Methodology | DMAIC (Define, Measure, Analyze, Improve, Control) | 5S (Sort, Set in Order, Shine, Standardize, Sustain) |
Goal | Reduce defects to less than 3.4 per million opportunities | Continuous, small-scale improvements |
Focus | Measurable financial returns | Employee engagement and empowerment |
Knowing the strengths and weaknesses of Six Sigma and Kaizen helps organizations choose the best Continuous Improvement Methodologies. This choice drives Process Optimization in their operations.
Implementing Continuous Improvement Initiatives
For Continuous Improvement (CI) to work well, you need a plan that covers everything. This means looking at how things work and how people work together. It’s all about making things better and keeping it that way.
Workforce Planning
Getting your team right is key for CI. You want people who can help make things better. This means:
- Knowing what skills you need for CI
- Finding and growing people with those skills
- Letting teams help improve things and share ideas
- Teaching them to think critically and solve problems
Performance Support
Having the right tools for Performance Support makes CI better. These tools give employees the help they need to do their best. Important parts of Performance Support are:
- Tools to help everyone do things the same way
- Tools to make sense of data and improve based on it
- Places to share knowledge and learn from each other
- Training when you need it most
“Successful Continuous Improvement programs focus on people and culture rather than just the actions to be taken.”
Case Studies: Continuous Improvement in Action
Organizations are working hard to get better at what they do. They’re using Lean Manufacturing, Six Sigma, and Kaizen to improve. These methods help make processes better and change the way companies work.
In the car industry, a big name had to cut down on how long it took to make cars and make them better. They used Lean Manufacturing to make their factory work better. They got rid of waste and made things flow smoother. This led to a 25% faster production time and a 15% better quality rate.
Key Performance Indicator | Before Lean Implementation | After Lean Implementation |
---|---|---|
Lead Time | 30 days | 22.5 days |
First-Pass Yield | 85% | 97.5% |
In healthcare, a hospital wanted to make patients wait less in the emergency room. They used Six Sigma to find and fix the problems. This cut down patient wait times by 40%, making patients happier and the hospital more efficient.
“Continuous improvement is not about the latest fad or the next big thing; it’s a way of life, a long-term approach to work.”
A company that makes industrial equipment had trouble keeping quality high. They started making small changes with Kaizen. This led to a 20% fewer defects and a 15% better use of equipment.
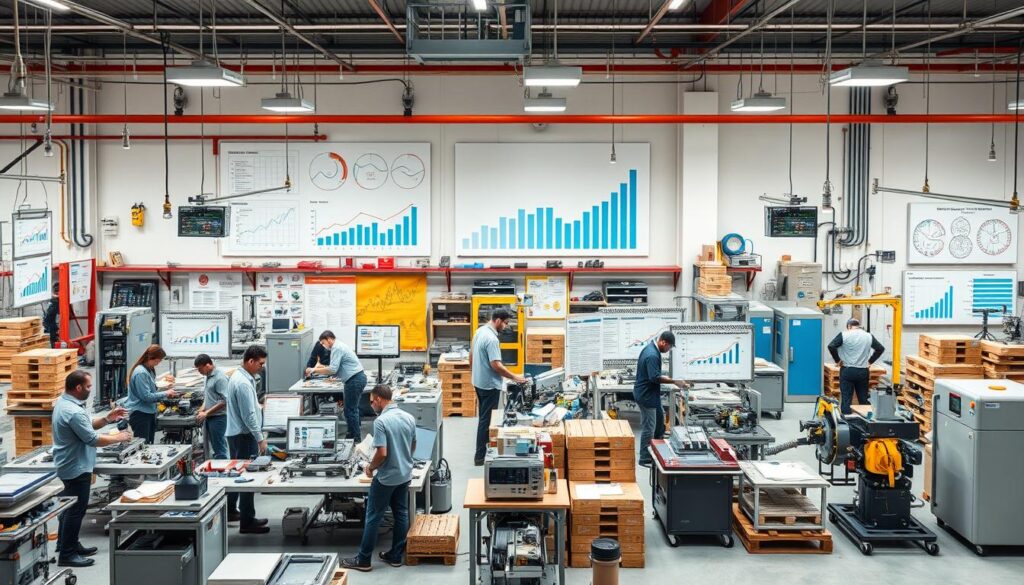
These stories show how Continuous Improvement can change things. By always learning and trying new things, companies can get better, make customers happier, and grow stronger.
Overcoming Barriers to Continuous Improvement
Creating a culture of continuous improvement in an organization can be tough. There are many challenges and barriers to face. It’s important to tackle the main issues that stop continuous improvement from succeeding.
One big problem is resistance to change. Employees might not want to try new things because they’re scared or worried about their jobs. Using strong change management can help. This includes talking clearly, involving employees, and listening to their worries.
Another big issue is lack of management commitment. If leaders don’t support continuous improvement, it’s hard to make it work. Building a strong organizational culture that values improvement is key to getting management on board.
Keeping employee engagement high is also vital. If workers don’t care or see the point, they won’t help much. Training, recognition, and chances to give feedback can make employees feel valued and involved.
“The key to overcoming barriers to continuous improvement is to address the root causes of resistance and foster a culture of continuous learning and improvement.”
By tackling these challenges with a solid plan, organizations can make a better place for continuous improvement. This leads to more success and lasting results.
Conclusion
Reflecting on our journey, the role of Gestion Industrielle (Industrial Management) is clear. Methods like Lean, Six Sigma, Kaizen, and Total Quality Management are key. They help manufacturing companies achieve process optimization and manufacturing excellence.
These strategies help cut waste and make workflows smoother. They also build a culture of continuous improvement. For industrial managers, using these methods is essential to stay competitive.
If you’re new to Industrial Management or experienced, exploring these tools is vital. It sets your organization up for success and adaptability. This way, you can excel in the changing world of manufacturing.
FAQ
What is Continuous Improvement?
Continuous improvement is a way to make a company better over time. It focuses on finding and fixing problems in current processes. The goal is to improve quality, cut costs, and make customers happier.
What are the key principles of Continuous Improvement?
The main ideas of continuous improvement are: – Finding and removing waste – Letting employees solve problems – Using data to make decisions – Creating a culture that always wants to get better – Using a cycle of improvement (like PDCA)
What are the benefits of implementing Continuous Improvement?
Continuous improvement brings many benefits. It makes things more efficient and of higher quality. It also cuts costs and makes customers happier. It encourages innovation and helps a company grow and stay competitive.
How do I measure the effectiveness of Continuous Improvement?
To see if continuous improvement is working, you need to track key performance indicators (KPIs). These KPIs should show how well you’re doing in areas like quality and cost. Methods like Six Sigma’s DMAIC help set up and track these KPIs.
What is the Six Sigma DMAIC process?
The Six Sigma DMAIC (Define, Measure, Analyze, Improve, Control) process is a way to make products better. It was created in 1986 by Bill Smith at Motorola. It uses data to check if processes are working well.
What are the key principles of Lean Manufacturing?
Lean manufacturing focuses on making things better. It was introduced by James P. Womack, Daniel Jones, and Daniel Roos. It has five main ideas: 1. Knowing what customers want 2. Getting rid of waste 3. Keeping production flowing smoothly 4. Making things only when needed 5. Always trying to get better
What is the Kaizen methodology?
Kaizen means “change for the better” in Japanese. It’s a way to get everyone involved in making things better. It uses brainstorming and the PDCA cycle to keep improving.
How do Six Sigma and Kaizen differ in their approach to Continuous Improvement?
Six Sigma and Kaizen both aim to improve things, but differently. Six Sigma uses data and focuses on reducing mistakes. Kaizen involves everyone and aims for small, ongoing improvements.
What are the key considerations for successfully implementing Continuous Improvement initiatives?
To make continuous improvement work, you need a plan that covers everything. This includes getting leaders on board and creating a culture of learning. You also need to train employees and make sure goals align with the business.
What are some common challenges in implementing Continuous Improvement?
Some big challenges include getting people to accept change and getting leaders to support it. It’s also hard to find the right KPIs and to keep the momentum going. Other issues include siloed thinking and not having the right skills or resources.